About The Pretreatment Directory
This tool was launched in November 2018 by The Composting Collaborative team. Submit questions, suggestions for updates and new profiles to info@compostingcollborative.org.
Pretreatment systems (sometimes called “preprocessing systems”) treat or process organic food waste onsite through biologic or thermal means. There are two general categories for pretreatment systems – wet and dry.
Aerobic digesters, also referred to as liquefiers or biodigesters, are wet systems using fresh water to dilute solids in combination with microorganisms to “digest” food waste into a liquid effluent that can be sent “down the drain” via sewer to a wastewater treatment plant, now more commonly referred to as a “wastewater resource recovery facility” (“WRRF”), or pumped to a holding tank for transport to third-party locations like an anaerobic digestion facility, a commercial composting site or a WRRF that accepts “outside” food waste (not conveyed via sewer).
Dehydrators and accelerated composters are dry systems. They dehydrate food waste through high temperature heating or through slow turning and agitation over a longer period of time. Outputs from dry systems can be cured into mature compost onsite or transported to a dedicated compost manufacturing facility. Dry output is sometimes also used for livestock bedding on farms or as an input for animal or fish feed.
Who uses pretreatment systems?
Pretreatment systems are great for organizations that produce large quantities of food such as:
- Universities
- Corporate Campuses
- Grocery stores
- Food service organizations
- Sports stadiums
- Music venues

Wet Systems
Aerobic digesters, biodigesters – These systems commonly referred to as “down-the-drain” systems are often confused with shredders, pulpers or garbage disposers. However, their main mechanism of action is through aerobic digestion of food waste. They do not require food to be preprocessed although some users may shred food waste to size reduce prior to feeding the unit. Depending on the company, biodigesters use microorganisms along with an auger to consistently turn material, which increases the surface area for microorganisms to break solids down into a nutrient dense liquid. This liquid is screened prior to being released down a drain leading to the sewer system for further processing by a WWRF. Some companies, like ORCA use plastic “biochips” that aid in the maceration of solids and also help to retain the colonies of microorganisms between loads when the unit is inactive. These systems can be continuously fed as they can process a full load of food waste in 24-48 hours. Compostable packaging and food service ware cannot be processed in aerobic digesters, though some can tolerate low amounts of uncoated paper items.
Pulpers, liquefiers – Unlike biodigesters that use microbes, water and agitation to treat food waste, these units use water and high speed blades to physically eviscerate food waste into small very small pieces. Pulpers are designed to dewater the slurry to produce a wet but not liquid output that can be composted on or offsite. Liquefiers are designed to either send a slurry down the drain or potentially to a containment tank for hauling to an anaerobic digestion (AD) facility or a commercial compost manufacturer. Note: None of the companies manufacturing or selling pulpers and liquefiers responded to our requests to participate in the Pretreatment Directory.
Dry Systems
Dehydrators – Process food waste in batches / cycles as opposed to continuously like wet systems and use electricity to heat material to approximately 180°F to 300°F, depending on the manufacturer, removing 80-90% of moisture from the food through evaporation. Units typically have paddles, augers or double-helix blades that continuously stir the material, making sure that heat and air flow is evenly distributed. Dehydrators are reported to reduce food weight and volume by up to 90%.Dehydrators will tolerate 1% to 15% of compostable materials including packaging and food service ware. However, some vendors recommend shredding compostables for better assimilation with organic material, to expedite the composting process, to ensure faster more thorough drying, and a more consistent output material. Dehydrators do not require additional water or enzymes be added to treat food waste. The output is subjected to a temperature that effectively kills all known pathogens, which is required for storage and handling. The output is a dry material with approximately 10% moisture that can be used for various purposes. Some manufacturers use it for livestock bedding on farms or as an input for animal or fish feed, but most cure the output onsite or send it to other composting facilities to manufacture into fully cured compost. The dehydrated output is not compost and if it becomes wet it will return to a composition similar to untreated food waste. Unlike most digesters that discharge an effluent into the sewer, dehydrators discharge a sterile, filtered water that can be discharged into a sewer or reused / recycled in gardens, landscaping or for cleaning trash bins.
Accelerated Composters – Are a subset of “in-vessel” composting systems which can range from small to very large capacity vessels. Accelerated composters are typically drum type systems that rotate very slowly on a fixed axis, stimulating microbial activity, and are capable of rapidly producing a soil amendment in 5-7 days (hence the term “accelerated”) or a fully cured compost over a period of many weeks. Traditionally, drum vessel systems were marketed to users to produce fully matured compost. One customer audience is commercial composters who can use these systems as a means of pretreating or “accelerating” the composting process prior to final curing via aerated static piles or windrows. The primary benefit being faster throughput times, allowing manufacturers to process more compost in less time.
More recently, manufacturers of drum systems are marketing units with smaller footprints to food waste generators (universities, restaurants, corporate campus cafeterias, etc) to process organics for either onsite or offsite uses. Some manufacturers are claiming that these smaller systems can make “compost” within 1-2 weeks, but there is no evidence to suggest that the output is significantly different than that which is produced by dehydrators. Users of accelerated composters can opt to produce a soil amendment in 1-3 weeks or depending on the volume of organics being generated, purchase a larger unit capable of processing materials over a longer period of time to produce cured compost.

Benefits of Pretreatment Systems
The primary benefit of using pretreatment systems is their ability to significantly reduce the volume and costs of managing food waste. “Down the drain” wet systems eliminate storing and hauling entirely unless the operator pumps the slurry to a containment tank for hauling off-site. Dry systems can reduce the volume of materials between 80-90%, significantly reducing hauling costs if being further processed off-site or sent to a landfill. Dry systems also significantly reduce odor and pest nuisances during storage periods between pick-ups from a hauler.
The ability of dry systems to significantly reduce the volume of material and to effectively control odors and pests (insects, rodents, wildlife in suburban/rural areas) has created the potential for food generators in more densely populated urban and suburban environments to store materials for longer periods of time before hauling off-site or for curing the output into mature compost on-site or, alternatively, for immediate use by mixing it with soil or purchased compost for on-site uses (landscaping, herb, vegetable gardens, sell as a product). If the output cannot be processed on-site, many fewer trucks are required to haul to off-site locations within or outside of the city. The table below is a comparison of some of the potential benefits of dry and wet systems.
Dehydrators / Accelerated Composters |
Biodigesters / Liquefiers |
|
Volume reduction | 80-90% | 100% |
Odor and pest control | Significantly reduced | Virtually eliminated |
Resource consumption | Electricity to turn material and to produce heat for evaporation | Electricity and water for dilution and conveyance of slurry |
Moisture content of output | Approximately 10-20% | Greater than 95% |
Management of outputs | 1) Onsite composting
2) Onsite mixing with cured compost or soil 3) Hauling to off-site composting
|
1) If sent to a Wastewater Resource Recovery Facility (WRRF)
What is fate of Biosolids?
2) If sent to Anaerobic Digestion
Fate of digestate?
|
Space requirements (size of units, food waste containers, storage area for processed materials) |
|
|
Degree of control/assurance that output goes to building soil or soil fertility | High | Low |
Operating costs |
|
|
Convenience of managing organics | Convenient | Very convenient |
Potential Return on Investment (ROI) from outputs | High
Potential input for: Animal bedding, animal or fish feed, pyrolysis, fuel pellets |
Zero, unless:
|
Flexibility to use outputs for multiple purposes | High
Multiple potential end uses:
|
Limited
|
Supports building a more robust infrastructure for compost manufacturing | Yes | Uncertain Potential |
Issues to Consider When Purchasing a Pretreatment System
There is not a “one size fits all” solution for pretreating food waste using these types of technologies. Choosing the right system depends on the circumstances of each business or even each location planning to use them. Some relevant questions a prospective operator should ask prior to purchasing a system are:
What is the primary reason for employing a pretreatment system in your operations?
- Cost reductions
Reduce the amount of materials and associated costs to haul material to a landfill. Down the drain technologies eliminate storage and hauling costs but in some cities may incur increased expenses related to discharge of effluent to sewer systems. Dehydrators significantly reduce the storage needs of food waste and the transportation cost to haul material off-site compared to initial quantity.
-
- Diversion from landfill:
Contract with a compost manufacturer or AD operator to haul off-site for use as feedstock.
-
- Produce energy and/or compost on-site:
Depending on the operators’ circumstances, both dry and wet systems can be used for on-site processing as an initial step for composting, or to produce energy and mature compost from digestate via anaerobic digestion.
How much physical space is available for processing output?
- If none or very limited, wet systems may make more sense for your operations but be sure to check with your local wastewater authority to understand if there are any restrictions, required registration of systems, or permits and fees associated with using a wet system.
- If space is available to store output for off-site hauling or for further processing on-site, dry systems are a good option. It’s helpful to factor in the reduction of space needed to store trash when calculating what space you may need to store dehydrated food waste before its hauled off-site. If half of your waste is food material that is size-reduced by 90% and you can shift from having two trash dumpsters to one, then you have new space to reallocate to this new stream. Wet systems with a containment vessel are also a good option if there is an AD operator in your area.
Are there any existing constraints for using wet systems?
- Check with local authorities to see if there are any restrictions for the use of down-the-drain systems (e.g., need to register prior to use or requirements to provide annual effluent testing results, etc).
- Permits may be required and additional fees may apply to account for dramatically increased volume of total suspended solids (TSS) and biological oxygen demand (BOD) that WRRFs must process.
- Check with your wastewater authority to see if they compost or land apply biosolids or “digestate” (liquid and solids produced from anaerobic digestion). If they do not and your company is committed to keeping valuable nutrients out of landfills, you will want to focus on the benefits that dry systems offer.
Are there any existing constraints for using dry systems?
- Output is not compost and must be cured further to produce a fully mature product. Output can be mixed in a ratio of one part dehydrated material to 7-10 parts soil or with cured compost make a beneficial soil amendment for on-site uses.
- If output gets wet, the dehydrated food becomes re-hydrated and is considered “biologically active” increasing chances for foul odors, pests and potential growth of pathogens.
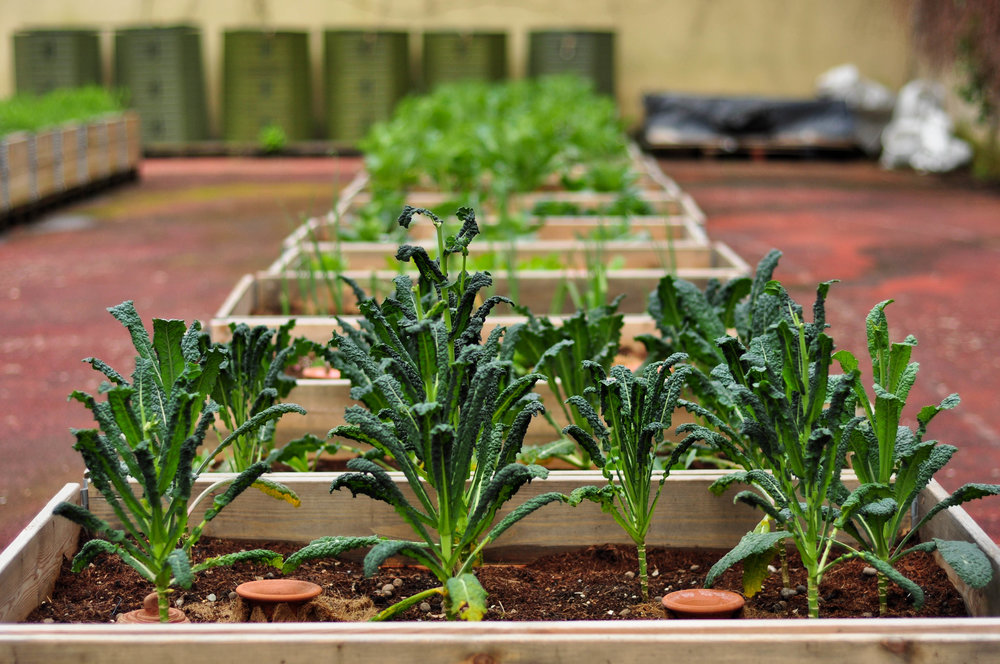
Maximizing the Return on Investment
Pretreatment systems can be a substantial outlay for small and medium-sized businesses especially. The primary cost savings are significantly reduced hauling costs if sending to landfill. There can also be possible further cost reductions if contracting with a compost manufacturer to haul because in some markets, composters’ tipping fees may be lower than landfilling to assure they are a competitive option. Liquefiers and biodigesters eliminate storage and hauling costs so the margin for cost avoidance is very high. Dehydrators reduce volume so significantly that many businesses may be able to glean further cost savings by downsizing space dedicated for storage or the number of trash vessels (e.g., fewer dumpsters or smaller dumpsters). If businesses plan on processing outputs on-site, they can capture even more cost savings by eliminating off-site hauling expenses as well as any cost savings from producing their own compost for landscaping, vegetable or herb gardens. There may also be an opportunity to earn revenue by selling class A compost or as input material for livestock bedding, animal or fish feed, or as a feedstock for pyrolysis (e.g., biochar) or pellet fuel. The New York State Pollution Prevention Institute at the Rochester Institute of Technology did an analysis of one dehydration technology and reported that if the output could be sold for a profit as an input to fish feed that the cost of processing one ton of food waste could be as low as $11 per ton.
For more densely populated urban and suburban areas, dehydrators and accelerated composters could facilitate more on-site composting of food waste at the point of generation, providing a valuable source of densified nutrients that can be integrated into a system of urban gardens to help decrease food deserts or to produce fresh vegetables for school lunch programs or area food banks. Pretreatment systems may also allow solid waste coordinators to capture and recycle food waste from more challenging environments like multi-family dwellings. The opportunities for teaching multiple audiences about the value of recycling their food waste into soil to grow food for increased health and community resilience are limitless.
Maximizing “Return on Environment”
In addition to the potential economic benefits, pretreatment systems could also be a valuable enabling technology for diverting more food waste from landfills, providing significant environmental benefits. Prospective buyers can refer to a very useful resource developed by FOR Solutions to help institutions such as universities to calculate not only the financial return on investment but also what they refer to as “return on environment” (“ROE”). Forty percent of food in the U.S. is never eaten, costing $165 billion in waste and is a major contributor to greenhouse gas emissions. The U.S. EPA estimates that food waste makes up 22% of our municipal solid waste stream with only 5.3% being diverted from landfills or incinerators.
Food waste is one reason that landfills are the third largest source of methane emissions, a greenhouse gas 21 times more potent than carbon dioxide. The U.S. EPA has set a goal of diverting 50% of the food waste generated in the U.S. by 2030. EPA advocates a multi-faceted strategy for meeting this goal and has developed a food waste recovery hierarchy to identify the highest and best use of these nutrients.
Unfortunately, there is some evidence in states, counties, or cities that have instituted landfill bans for organics that some businesses are using pretreatment systems solely to reduce the volume of material to stay below mandated limits. The dehydrator analysis conducted by the New York State Pollution Prevention Institute at the Rochester Institute of Technology reported that if dehydrated food waste is disposed of in landfill, the cost of processing one ton of food waste may be as high as $133/ton. That is significantly higher than the nationwide average tip fee of $51.82 as reported from a 2017 study by the Environmental Research & Education Foundation (EREF) of 400 municipal solid waste landfills which does not even include the costs of hauling fees. For those that don’t value the potential environmental benefits that pretreatment systems could provide, perhaps a poor economic return on their investment will be more convincing. Calculating a Return on Environment is important because one of the primary benefits of pretreatment systems is their potential to help divert a significant volume of food waste from landfills.
Unanswered Questions Remain About Both Wet and Dry Systems
A major concern of the composting community regarding the use of wet systems is that there is no guarantee that food waste sent down the drain for treatment by water resource recovery facilities (WRRFs) will make their way back to the soil. There is a lack of current data on biosolids end use and disposal. Earlier studies conducted by the North East Biosolids and Residuals Association (NEBRA) and partners based on 2004 data estimated that 55% of the nearly 7.2 million dry tons of biosolids generated were land applied for agronomic, silvicultural or land restoration projects. NEBRA also estimated that about 23% were treated to meet Class A requirements as a soil amendment and 34% treated to meet Class B requirements. (footnote: NEBRA, 2007. A National Biosolids Regulation, Quality, End Use and Disposal Survey, available at https://www.nebiosolids.org/about-biosolids/). In 2010, BioCycle and NEBRA collaborated to collect updated data and estimated that 7.8% of biosolids were being composted. (footnote: Beecher, N. and N. Goldstein. 2010. Biosolids composting in the United States – 2010 update. BioCycle, December 2010).
In 2017, the EPA surveyed U.S. operators of anaerobic digestion facilities (WRRF digesters, stand-alone AD operations and on-farm digesters) and reported end uses for solid digestate from the facilities surveyed. Of the 1,200 WRRFs in the U.S. with anaerobic digesters producing biogas, EPA confirmed that 78 WRRFs were accepting “outside” food waste and co-digesting the food waste with the wastewater solids collected through their sewer systems. Fifty-eight stand-alone digesters were also confirmed as operational as well as 18 on-farm digesters.
EPA asked how facilities reused solid digestate. 76% of solid digestate produced by WRRFs went to beneficial uses while 25% went to landfill, incineration or “other” (11%). For stand-alone digesters, 63% went to beneficial uses, while 13% was landfilled and 35% went to “other”. Table 20 and Figure 10 from EPA’s report provides an overview of the top five end uses for each type of facility.
Some envision the most efficient and environmentally beneficial method of recycling food waste is to use the nation’s sewer systems to convey food to WRRFs with the eventual goal of upgrading all wastewater treatment facilities to produce biogas. They surmise that pretreatment systems such as biodigesters in combination with state or federal policies mandating composting or land application of biosolids and digestate as the least carbon intensive method of meeting EPA’s 50% reduction goal by 2030, and significantly scaling the recycling of food waste back into soil. But many unanswered questions remain about the ability of the nation’s sewer infrastructure to accommodate such a vision:
-
- Many cities’ sewer infrastructure are aging, are in need of repair and/or have not been designed to convey effluents with higher levels of solids. Localities are also concerned that there may be an increase in fats, oils and grease (“FOG”), potentially resulting in more “slugs” in sewer lines, leading to costly repairs for tax payers.
- Concerns that food waste will be contaminated by being mixed with all other materials that go into sewer systems (e.g., toxic chemicals, pharmaceutical residues from human waste, motor oil, paint, oil residue from roads, etc.).
- During stormwater surges, combined sewer system overflows will send effluent directly to open waters. The concern with increasing the amount of food waste conveyed by sewers is that during overflow events, organics will be diverted from wastewater treatment plants, and the beneficial value of biosolids or digestate are lost.
A point of confusion for many considering dry systems has to do with the marketing claims that some manufacturers have made about the physical properties or quality of output their systems will produce. Most refer to output material as a “soil amendment” but some use the term “compost”. Another point of confusion are claims about the timeframe in which these units will manufacture an output equal in quality to mature compost. Composting is a dynamic process with very few concrete demarcations for when organic matter transitions through the various stages of decomposition to fully “matured” or “cured” compost. When typical indices for measuring compost maturity (temperature, moisture, pH, carbon/nitrogen (C/N) ratio, total carbon, % organic matter and organic nitrogen) are plotted against a time scale, the average number of days required to reach maturity is on the order of 40-180 days and is highly dependent upon the feedstock mix, method of composting and the quality of end product desired. Compost manufacturers’ claims can range from 90, 180 days, or more to produce a high quality compost. Whether it is 40, 90 or 180 days to produce a fully matured compost, these are much longer timeframes than the 5-14 days that some of the pretreatment system manufacturers claim. By rapidly heating food waste to evaporate 80-90% of the moisture content and effectively killing pathogens, dehydrators and accelerated composters may reduce the amount of time that organic matter spends in the initial stages of composting but they cannot produce an output considered to be “compost” without further treatment of the material for several more weeks until full maturation is achieved. As previously mentioned, while dehydrated materials or those from accelerated units not fully composted, they can be used immediately and safely as soil amendments if mixed in a ratio of 1 part processed material to 7-10 parts soil or cured compost.
Conclusion
The Composting Collaborative prepared this guidance document as a supplement to the Pretreatment Directory because of the amount of confusion in the marketplace about pretreatment systems. The confusion is partly due to different terms used for similar technologies, how they work, the value of the output they produce, and marketing claims that are sometimes at odds with the science of composting. Despite this confusion, many members of the Composting Collaborative see the potential for pretreatment systems to play a significant role in our ability to create a more sustainable infrastructure for converting unavoidable food waste into valuable sources of energy and/or nutrient rich soils as opposed to continued global warming methane emissions. Like all technologies, the benefits can be enhanced and impacts minimized by studied application of these systems. The Composting Collaborative will continue follow and explore the value that these types of technologies can offer for creating a more sustainable infrastructure for managing unavoidable food waste and other organics.
Related Resources:
- RecyclingWorks Massachusetts – On-Site Systems for Managing Food Waste, updated 2017
- BioCycle Magazine: On-Site Food Waste Treatment by Nora Goldstein and Charlotte Dreizen
- BioCycle Magazine: Analysis of Biodigesters and Dehydrators to Manage Organics On-Site Part 1 by Zoe Neale.
- BioCycle Magazine: Biodigesters and Dehydrators – Operational Experiences Part 2 by Zoe Neale.
- CalRecycle Organics webpage
- Compostable Materials Handling Operations and Facilities Regulatory Requirements
- Food Service Equipment Reports